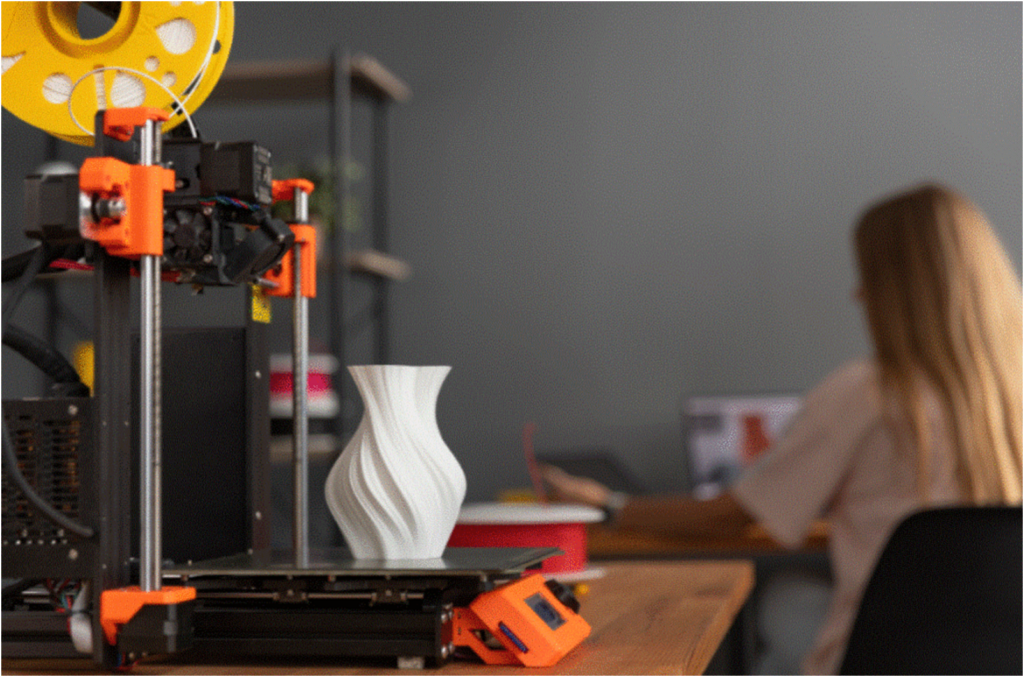
INTRODUCTION
FDM (Fused Deposition Modeling) technology is one of the most widely used 3D printing technologies. It works by melting thermoplastic filament and layering it to create objects. This article explores the principles, advantages, disadvantages, and various applications of FDM technology.
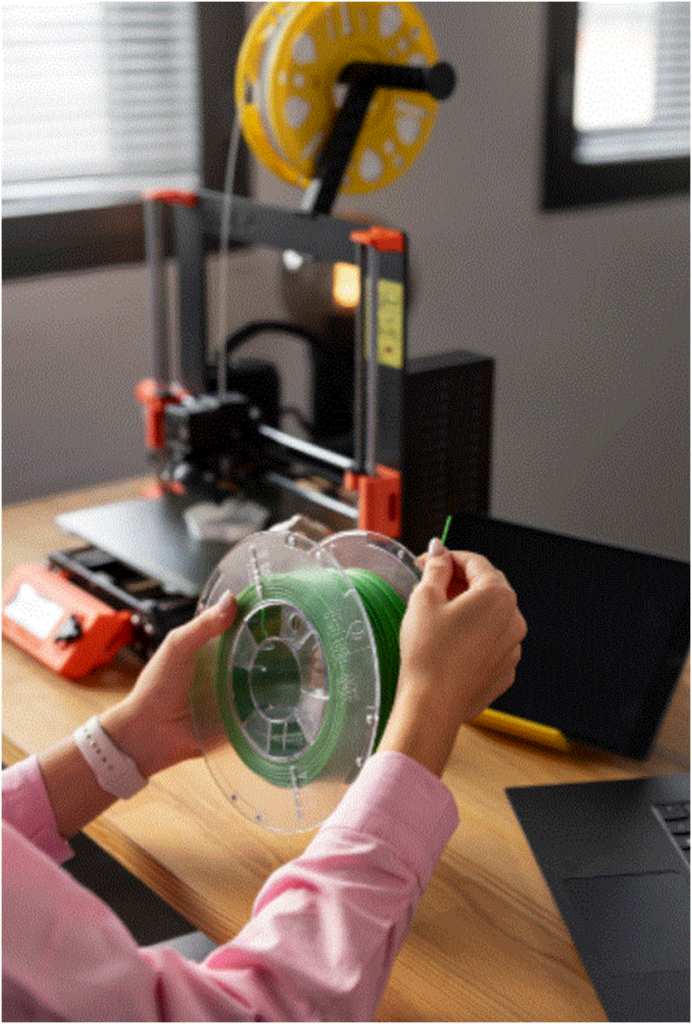
Principles of FDM Technology
FDM technology operates through the following process:
- Filament Feeding: Thermoplastic filament is fed into the printer head.
- Heating and Extrusion: The filament is heated in the printer head, turning it into a liquid, which is then extruded through a nozzle.
- Layer Stacking: The extruded material is layered on the bed to form a 3D model.
- Cooling and Solidification: The layered material cools and solidifies.
Advantages of FDM Technology
- Cost-Effective: FDM printers are relatively inexpensive.
- Ease of Use: Simple to use and easy to maintain.
- Material Variety: Can use various thermoplastics like PLA, ABS, PETG, etc.
Disadvantages of FDM Technology
- Surface Quality: Layer bonding can result in a rough surface.
- Accuracy: May have lower accuracy compared to other 3D printing technologies.
- Production Speed: Can take a long time to produce large objects.
Applications of FDM Technology
- Prototyping: Quickly create prototypes in the early stages of product development.
- Education: Used in schools and universities for 3D printing education.
- Consumer Products: Suitable for custom products and small-scale production.
Conclusion
FDM technology is a core technology in 3D printing, widely used in various fields. It is cost-effective and easy to use, making it suitable for everyone from beginners to experts. FDM technology is expected to continue advancing and finding new applications in the future.